Customer Success: Manufacturing
Building Better Fish Processing Machinery with Curio ehf.
Machine: OMAX 55100, MAXIEM 1530
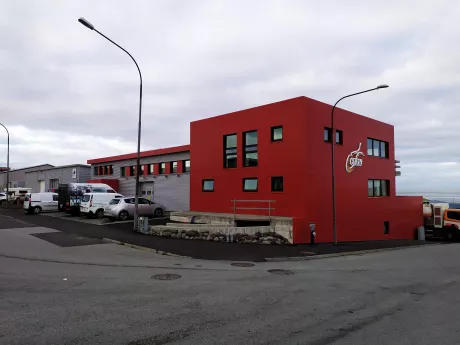
In Hafnarfjordur, Iceland, Curio ehf. builds five different machines for fish processing with the help of four OMAX-brand waterjets.
Whether filleting, skinning, or heading, each of Curio’s machines come in a range of sizes that handle fish up to 18 kg (39.6 lbs). Curio touts that it brings “devotion inherent in handmade machinery parts, technical innovation and Icelandic ingenuity – and with this magical mix we assemble potent seafood processing machines with a strong character and a great performance.” In addition, the company offers a sharpening machine that hones the circular knives used in the company’s other machines. Curio’s products are renowned for their reliability as well as their ability to provide better processing yields with accurate cutting.
“The company started in 1994 thanks to the lifelong enthusiasm and interest in fish processing machinery of the founder, Mr. Ellidi Omar Hreinsson,” said Steinmar Gunnarsson, production manager for Curio. “In the early years, the intention was only to have three to four people working in the company and the goal was to keep it small – but enough to support the owner and employees’ families.”
Nevertheless, when the demand for Curio’s highly efficient machines grew, the company brought on more employees, added locations, and acquired more advanced equipment. Currently, Curio employs more than 40 people in Iceland, Scotland and Norway.
In 2006, Curio purchased its first waterjet, the OMAX 55100 Precision JetMachining Center. The OMAX 55100 is the industry-standard workhorse for high-speed precision machining.
“Initially, the first waterjet was purchased to produce fish processing machinery on a relatively small scale,” explained Gunnarsson. “The biggest advantage is the cleanliness of the cutting process. Second is the fact that there are no emissions – air contamination – from the process. All you need is electricity, water, compressed air and abrasives.”
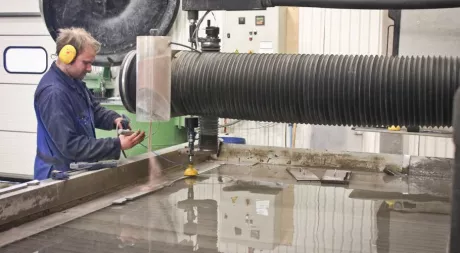
The advantages of waterjet cutting over other cutting methods are numerous when it comes to environmental effects for those who work in the vicinity of the waterjets. Compared to other manufacturing tools, waterjets are relatively quiet – usually working at around 75dB. There are no chemicals, oils, or solvents involved that may contaminate workpieces or injure operators. Cutting underwater allows for cleaner, safer cutting. Furthermore, the OMAX direct-drive pumps don’t incorporate a hydraulic system, which allows for easier maintenance and longer mechanical life.
The precision, accuracy and speed of the OMAX waterjet, especially when cutting very thick stainless steel, was a massive benefit for Curio. “It started with the old 55100 – the first waterjet in Iceland! – but as the production expanded, the need for more waterjets arose,” said Gunnarsson. In 2014, Curio added a MAXIEM 1530 to their production floor.
Usually, Curio uses its waterjets to cut stainless steel from sheets, either 1.250 mm x 2.500 mm (4 ft x 8 ft) or 1.500 mm x 3.000 mm (5 ft x 10 ft). With each sheet, the company produces an array of parts for the processing machines. Their cut times last as long as 26 hours.
“When cutting thin materials, although lasers are quicker, there is no hardening of the edge during the [waterjet] process, and post-processing edges is quick and easy,” explained Gunnarsson. Though Curio primarily cuts food-grade stainless steel, it also uses its waterjets to cut aluminum as well as polyoxymethylene (POM) and polyethylene high-density (PEHD) plastics up to 30 mm (1.18 in.) thick. As Gunnarsson said, “Waterjets can cut through any material, metals, plastic, wood, glass – virtually anything that can be fastened to the cutting table.”
The MAXIEM 1530 gave Curio a boost, but the company still needed more. In 2019, it added an additional two OMAX 60120s, both with 100 hp pumps. These robust and reliable systems require little maintenance and are as easy to use as conventional machine tools, particularly with a bridge-style Y axis for unobstructed material loading.
“By purchasing the two new 60120 machines, we feel very confident we will stay on top as far as competitiveness goes in the industry,” said Gunnarsson. “Curio will be better prepared to produce and sell more varieties of machines, with the increased production