Tips & Tricks
IntelliMAX-Think Smarter
Cutting with a CNC tool such as a mill can be fairly straightforward, as there are lookup tables, machinist handbooks, and simple formulas to use in order to determine cut speeds for a particular material. For flexible cutting tools, such as plasma, laser, and waterjet, these calculations quickly become very complex as the cutting stream flexes and changes shape depending on how fast the nozzle moves. The complexity of calculations becomes even more difficult when part geometry is taken into consideration, and all these challenges need to be factored in the controller software.
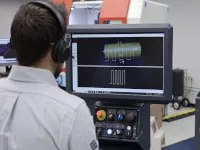
Given this complexity, the best solution is an integrated software system such as the OMAX IntelliMAX® Software Suite. Developed by Dr John Olsen and Carl Olsen from the idea of compute first then cut, the IntelliMAX software is the first software specifically designed for waterjet machining. With the software engineers working side by side with the mechanical engineers, coupled with constant access to test machines and highly skilled application specialists, the IntelliMAX software has the most evolved waterjet cutting model available. Developed through in-depth theoretical research that was then tested and modified through comprehensive practical application, the IntelliMAX cutting model, currently on its 4th version, routinely and consistently lets OMAX waterjet systems cut faster and cleaner than non-integrated software systems, maximizing your shop’s production.
Another advantage to having an integrated software system is that it allows for a better understanding of the mechanics of cutting, which helps when you are cutting a new, distinctive material where its cutting properties might not be known. OMAX technical support also has direct access to both the hardware engineers and software engineers, so unique material cutting challenges can be solved far more quickly, and often times be added to future software releases.
Beyond the cutting advantages, an integrated software package like IntelliMAX also incorporates other highly useful aspects of operating a machine tool, such as advanced system monitoring. An integrated system monitoring tool can keep your machine at optimal production with useful alerts for simple things such as a water pressure drop to adaptively scheduling pump rebuild times outside of production jobs to reduce potential machine downtime.
The IntelliMAX software also has a scripting engine to expand capabilities to improve production on OMAX waterjets. Integrated into IntelliMAX means operators can easily extend the software to do new things, such as modifying a cut path in MAKE, the machine controller software, or even create an application or plug-in. A common use for the IntelliMAX scripting engine would be to automate steps to reduce operator involvement, but other uses can extend capabilities beyond the common, such as synchronizing MAKE with a robot. With the ability to combine multiple scripts together into a single plug-in, levels of automation and shop customization are unlimited. With IntelliMAX, your waterjet machining can be specialized to fully integrate into your shop’s existing processes.
IntelliMAX provides all of these features and more and continues to set the standard for waterjet control software.